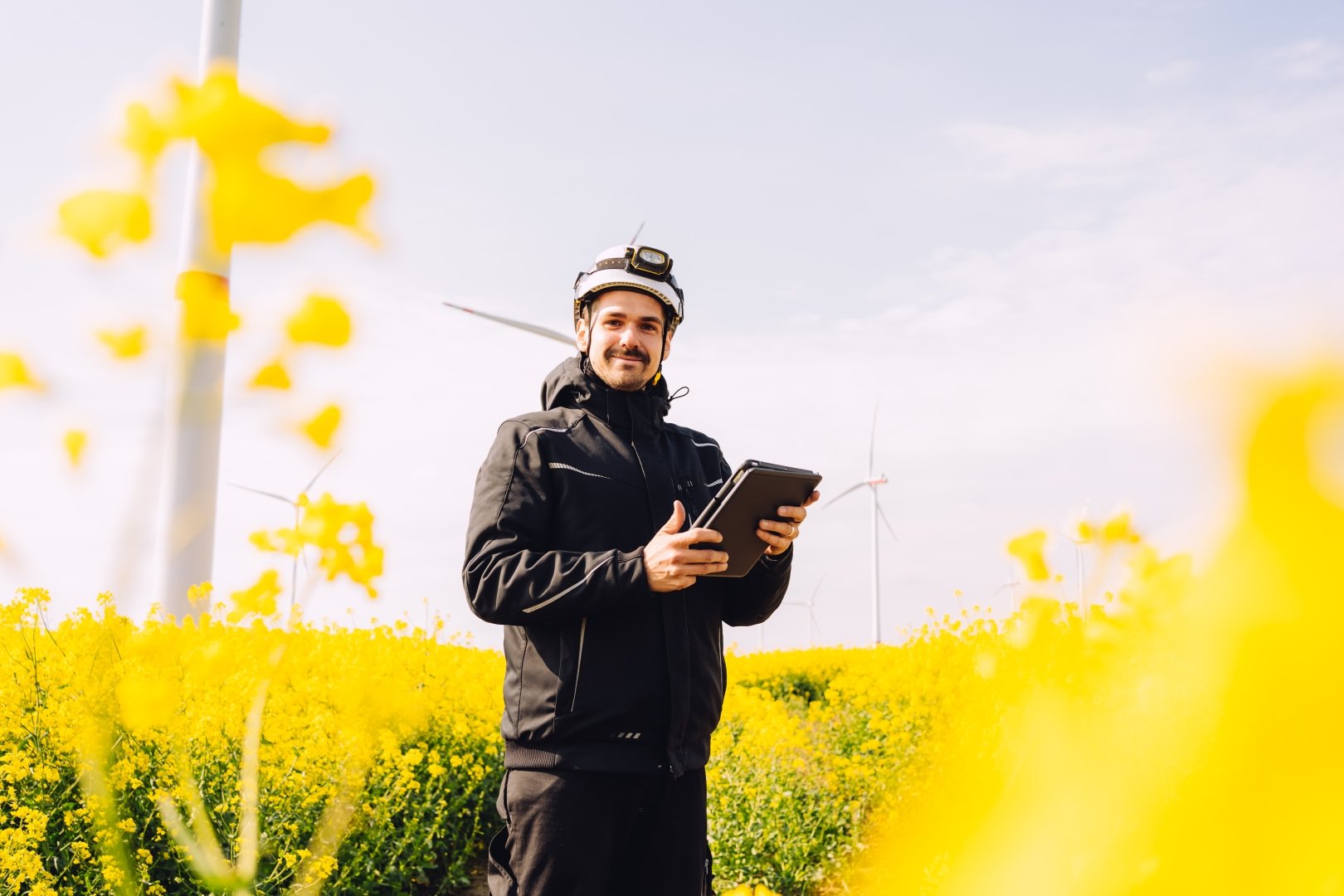
Test DGUV-V3
Entrevista a nuestro experto
Nuestra documentación para la inspección DGUV-V3
Pregunta 1: ¿Qué pruebas ofrecen como parte del test DGUV V3?
Kevin Gering:
Esta es una de las preguntas más frecuentes de nuestros clientes. La prueba DGUV-V3 incluye diversas pruebas para garantizar que su aerogenerador cumple los requisitos legales. No sólo comprobamos la seguridad eléctrica del aerogenerador, sino también los sistemas de media tensión y los dispositivos de protección, que son esenciales para el funcionamiento de todo el sistema. La estación de transferencia (ÜSt) también es un tema tratado con frecuencia: Aquí ofrecemos una prueba exhaustiva que garantiza que todos los componentes relevantes, como fusibles y cables, se someten a una prueba de funcionamiento tras la desconexión del sistema de media tensión. De este modo, cubrimos todos los requisitos de las pruebas y garantizamos el buen funcionamiento de su aerogenerador.
Una nueva incorporación a nuestra cartera es la comprobación del sistema externo de protección contra rayos conforme a la norma DIN EN 61400-24, que incluye la medición de la resistencia o la comprobación de la continuidad desde la góndola hasta el terminal de conexión a tierra en la base de la torre, subdividida en mediciones individuales en función del diseño, por ejemplo, para los descargadores de chispas. Una vez finalizada la prueba, el cliente recibe un informe independiente sobre la protección contra el rayo.
Ejemplo práctico:
Recientemente hemos llevado a cabo una prueba en un parque eólico, en la que se comprobaron los recorridos de los cables de la aparamenta. Aquí se prueban diferentes campos, incluido el transformador. Básicamente, estos cables nunca se prueban porque no está prescrito. Pero, afortunadamente, el cliente insistió en ello y así se descubrieron defectos y se evitó un incendio en el sistema.
Pregunta 2: ¿Qué cualificación tienen sus empleados para las inspecciones DGUV V3?
Kevin Gering:
La cualificación de nuestro personal es la clave del éxito de una inspección segura. Todos nuestros ingenieros de pruebas son especialistas en electricidad (EFK) con años de experiencia en pruebas de aerogeneradores. Nuestros equipos no sólo tienen amplios conocimientos de ingeniería eléctrica, sino que también cuentan con formación específica para operaciones de conmutación en sistemas de media tensión. Trabajan con equipos de medición de última generación, como dispositivos de medición de aislamiento y dispositivos de prueba de relés de protección, para garantizar resultados precisos y fiables. Esta experiencia nos permite probar incluso sistemas complejos de forma eficaz y segura.
Cualificaciones específicas:
Nuestros equipos presentan periódicamente certificados de formación y llevan más de diez años realizando pruebas. Esto incluye no sólo la inspección en sí, sino también un ojo entrenado para detectar posibles puntos débiles que otros pueden pasar por alto. Cubrimos más del 90 % del paisaje vegetal.
Consejo para los operadores:
A la hora de seleccionar a su socio de inspección, asegúrese de que los inspectores están demostradamente cualificados y tienen experiencia con la tecnología específica de los aerogeneradores. Un proceso de inspección mal realizado puede acarrear costosos gastos de seguimiento.
Pregunta 3: ¿Cuánto dura la inspección y cuándo están disponibles los informes?
Kevin Gering:
La duración de la inspección depende del tamaño y la complejidad del aerogenerador, de si se trata de una turbina antigua o de una más nueva que tiene muchos componentes eléctricos instalados en el buje, pero normalmente gestionamos hasta tres inspecciones in situ en un día. Si se detectan defectos importantes o problemas relevantes para la seguridad, informamos inmediatamente al operador para que podamos iniciar rápidamente las contramedidas. El objetivo es que el sistema vuelva a funcionar de forma segura lo antes posible. El informe de inspección, en el que se resumen detalladamente todos los resultados, suele estar disponible en un plazo de días laborables.
Pregunta 4: ¿Qué ocurre en caso de defectos?
Kevin Gering:
Si descubrimos defectos in situ, los comentamos directamente con el cliente y le hacemos recomendaciones para subsanarlos. Hace poco, pudimos resolver una situación potencialmente crítica detectando en una fase temprana daños por corrosión en un tendido de cables, sin que ello supusiera una interrupción importante de las operaciones.
Siguiente paso:
También nos aseguramos de informarle a tiempo del siguiente intervalo de inspección. Esto le da seguridad de planificación y le permite programar futuras inspecciones con tiempo suficiente para evitar tiempos de inactividad innecesarios.
Pregunta 5: ¿Qué pruebas se realizan durante la prueba DGUV-V3 para sistemas de baja tensión y por qué son tan importantes las mediciones ISO, la impedancia de bucle y la comprobación de la conexión equipotencial y la resistencia de tierra?
Kevin Gering:
Las pruebas DGUV-V3 de los sistemas de baja tensión de los aerogeneradores son cruciales para garantizar un funcionamiento seguro y sin problemas de los sistemas eléctricos. Estas pruebas no sólo ayudan a prevenir accidentes, sino también a evitar fallos que podrían causar costosos tiempos de inactividad del sistema.
Las mediciones ISO (mediciones de resistencia de aislamiento) son especialmente importantes para comprobar si los cables y componentes eléctricos están correctamente aislados. Un aislamiento deficiente puede provocar cortocircuitos y descargas eléctricas peligrosas, que pondrían en peligro tanto la seguridad de los empleados como la funcionalidad del aerogenerador.
La prueba de impedancia de bucle garantiza que, en caso de fallo, por ejemplo un cortocircuito, el mecanismo de protección (por ejemplo, fusible o disyuntor) responda con la rapidez suficiente para evitar lesiones personales o daños en el sistema. Si la impedancia del bucle es demasiado alta, es posible que los dispositivos de protección no se activen a tiempo, lo que podría tener consecuencias fatales.
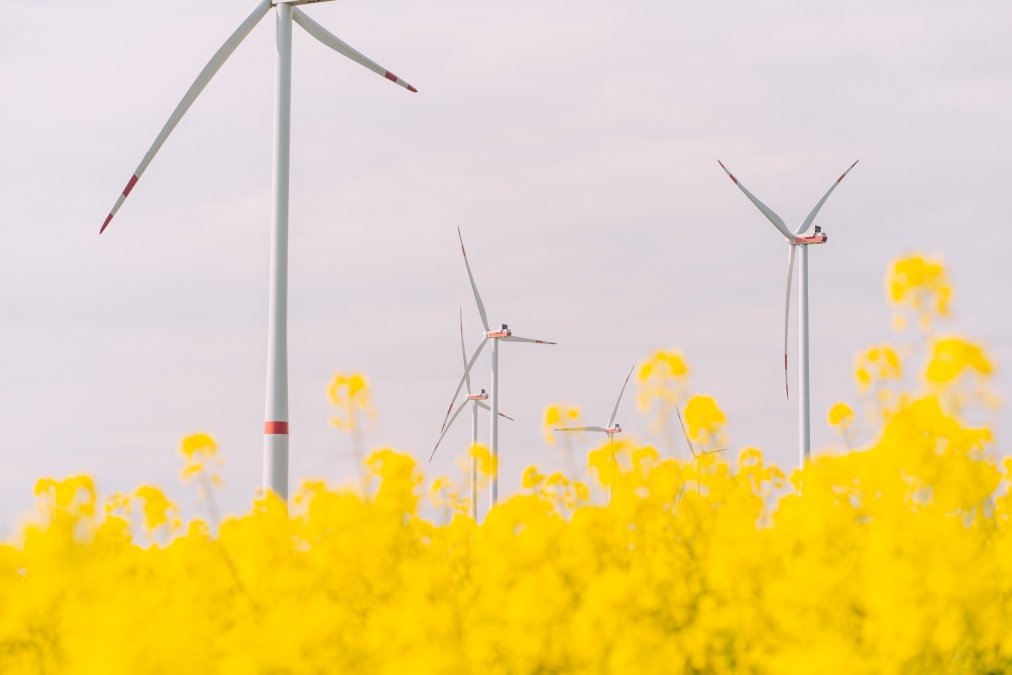
Comprobar la compensación de potencial es esencial para garantizar que todas las partes conductoras de una instalación tengan el mismo potencial eléctrico. De este modo se evita que se produzcan tensiones peligrosas que puedan poner en peligro a las personas o los equipos.
La resistencia de tierra se mide para garantizar que las corrientes eléctricas de defecto puedan descargarse a tierra de forma segura. Si la resistencia de tierra es demasiado alta, es posible que las corrientes de defecto no fluyan correctamente, lo que aumenta el riesgo de descargas eléctricas o daños en el sistema.
Además, siempre se realiza una inspección visual durante la prueba DGUV-V3 para reconocer y rectificar defectos evidentes, como cables dañados o conexiones sueltas, en una fase temprana. Todas estas medidas sirven para garantizar la seguridad operativa y la longevidad del aerogenerador y cumplir los requisitos legales.
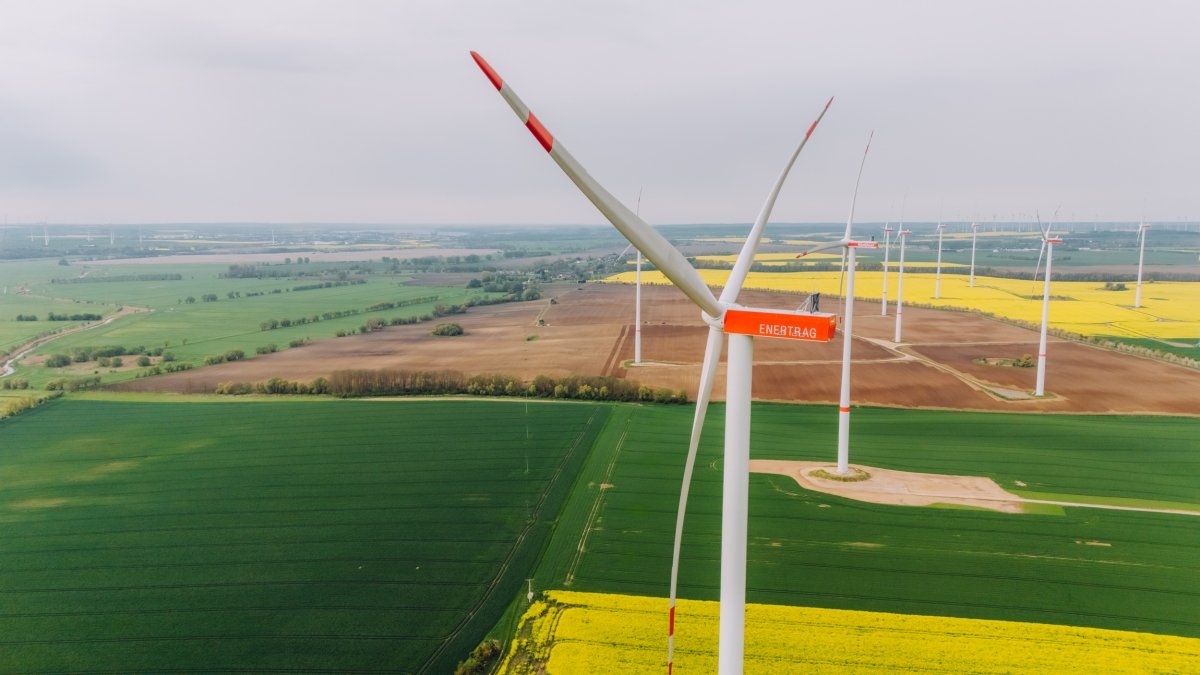
La prueba DGUV-V3 para sistemas de media tensión garantiza que todos los sistemas eléctricos funcionen de forma fiable y segura. Los requisitos de las pruebas son especialmente elevados en los sistemas de media tensión, ya que en ellos se utilizan tensiones más altas que pueden entrañar mayores peligros. Las pruebas principales incluyen
- Medición de la resistencia del aislamiento: Al igual que en los sistemas de baja tensión, también se mide la resistencia del aislamiento de los sistemas de media tensión para garantizar que no haya corrientes de fuga peligrosas que puedan provocar cortocircuitos o descargas de tensión.
- Pruebas de interruptores y transformadores: Estos componentes se someten a pruebas especialmente intensivas, ya que desempeñan un papel clave en la distribución y el control de la energía. Aquí se comprueba la funcionalidad y la capacidad de carga de los dispositivos de conmutación.
- Comprobación de la puesta a tierra y la resistencia a cortocircuitos: Para garantizar que el sistema está adecuadamente protegido en caso de fallos como cortocircuitos, se comprueba la puesta a tierra y la capacidad del sistema para descargar con seguridad altas corrientes de cortocircuito.
- Inspección visual y comprobación mecánica: Una inspección visual detallada de los componentes del sistema revela defectos evidentes, como daños mecánicos o conexiones incorrectas.
- Prueba de rigidez dieléctrica: se comprueba si el sistema se mantiene estable durante los picos de tensión y si no hay defectos de aislamiento.
La prueba de los dispositivos de protección desempeña un papel especialmente importante en las pruebas de sistemas de media tensión. Los dispositivos de protección se utilizan para proteger el sistema en caso de fallo y desconectarlo a tiempo. Aquí se realizan varias pruebas:
- Tiempo y corriente de disparo: se comprueba si los dispositivos de protección se disparan correctamente y dentro del tiempo prescrito en caso de sobrecarga o cortocircuito.
- Ajustes de protección: El ajuste de los dispositivos de protección debe corresponder a los parámetros de la red y a los requisitos del sistema. Se comprueba si están correctamente programados y calibrados.
- Pruebade funcionamiento: se comprueba si los dispositivos de protección se disparan de forma fiable en caso de fallos simulados, como sobrecorrientes o fallos a tierra.
La prueba de los dispositivos de protección es especialmente importante, ya que unos dispositivos de protección defectuosos podrían provocar graves daños o incluso el fallo de todo el sistema en caso de emergencia.