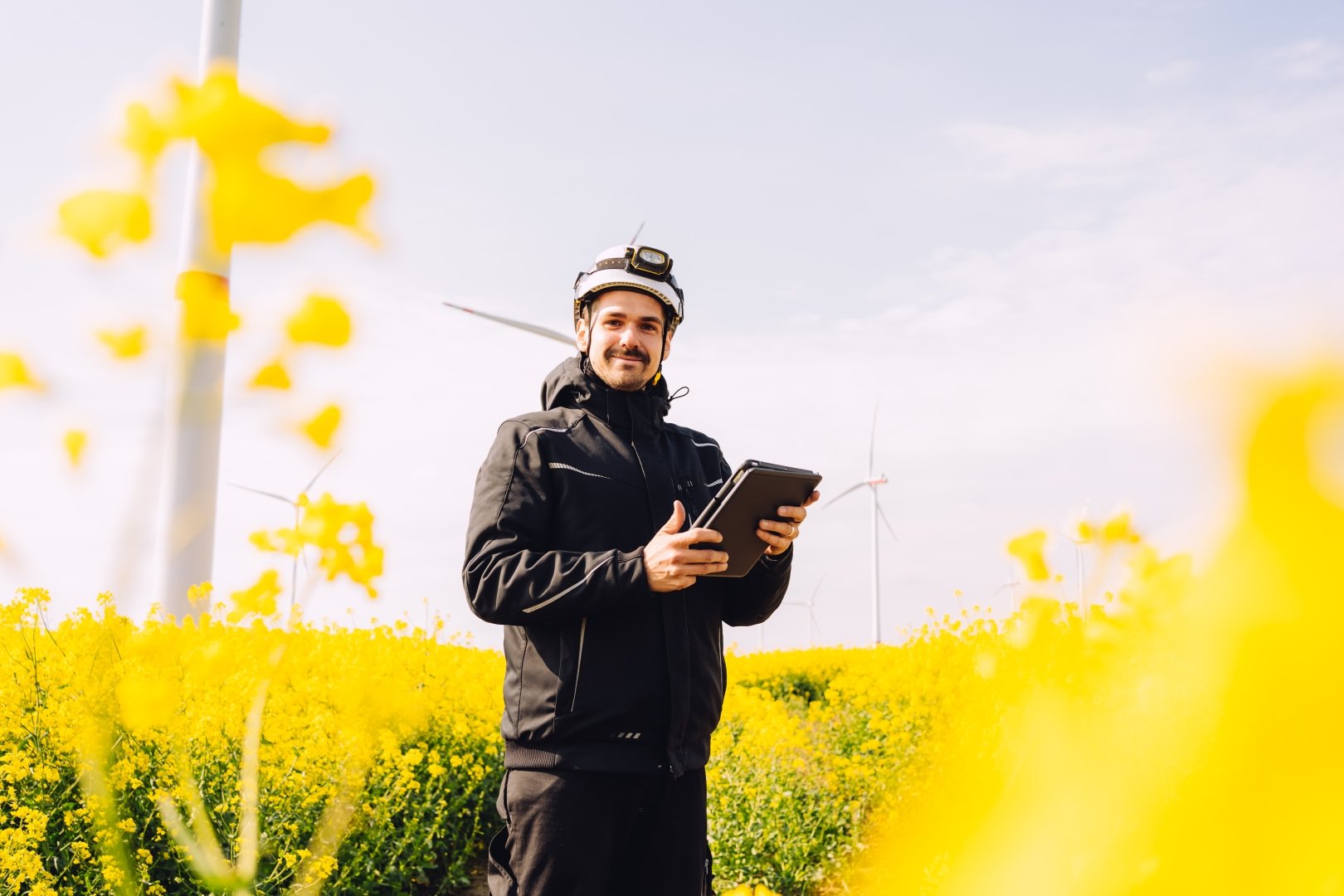
DGUV-V3-Inspection
Our expert interview
Our documentation for the DGUV-V3 inspection
Question 1: What tests do you offer as part of the DGUV V3 test?
Kevin Gering:
This is one of the most frequently asked questions from our customers. The DGUV V3 test includes a variety of tests to ensure that your wind turbine meets the legal requirements. We not only test the electrical safety of the wind turbine, but also the medium-voltage systems and protective devices, which are essential for the operation of the entire system. The transfer station (ÜSt) is also a frequently addressed topic: Here we offer a comprehensive test that ensures that all relevant components, such as fuses and cables, are tested for their function after the medium-voltage system has been switched off. In this way, we cover all testing requirements and ensure the smooth operation of your wind turbine.
A new addition to our portfolio is the testing of the external lightning protection system in accordance with DIN EN 61400-24, which includes resistance measurement or continuity testing from the nacelle to the earth connection lug in the tower base, subdivided into individual measurements depending on the design, e.g. for spark gaps. Once the test has been completed, the customer receives a separate lightning protection report.
Practical example:
We recently carried out a wind farm test, where the cable routes of the switchgear were tested. Different fields are tested here, including the transformer. These cables are basically never tested because this is not prescribed. Fortunately, the customer insisted on this and so defects were discovered and a fire within the system was prevented.
Question 2: What qualifications do your employees have for DGUV V3 inspections?
Kevin Gering:
The qualifications of our staff are the key to a successful and safe inspection. All of our test engineers are trained electrical specialists (EFK) with years of experience in testing wind turbines. Our teams not only have extensive knowledge of electrical engineering, but also have specific training for switching operations on medium-voltage systems. They work with state-of-the-art measuring equipment, such as insulation measuring devices and protective relay testing devices, to ensure accurate and reliable results. This expertise enables us to test even complex systems efficiently and safely.
Specific qualifications:
Our teams regularly submit training certificates and have been carrying out tests for over ten years. This includes not only the inspection itself, but also a trained eye for potential weak points that others may overlook. We cover over 90 % of the plant landscape.
Tip for operators:
When selecting your inspection partner, make sure that the inspectors are demonstrably qualified and have experience with the specific technology of wind turbines. An incorrectly performed inspection process can result in expensive follow-up costs.
Question 3: How long does the inspection take and when are the reports available?
Kevin Gering:
The duration of the inspection depends on the size and complexity of the wind turbine, is it an old turbine or a newer turbine that has many electrical components installed in the hub, but we usually manage up to three on-site inspections in one day. If major defects or safety-relevant problems are detected, we inform the operator immediately so that we can initiate countermeasures quickly. The aim is to get the system back into safe operation as quickly as possible. The inspection report, in which all results are summarized in detail, is normally available within working days.
Question 4: What happens in the event of defects?
Kevin Gering:
If we find defects on site, we discuss them directly with the customer and make recommendations for rectification. Recently, we were able to defuse a potentially critical situation by detecting corrosion damage to a cable route at an early stage - without any major interruption to operations.
Next step:
We also ensure that you are informed of the next inspection interval in good time. This gives you planning security and allows you to schedule future inspections in good time to avoid unnecessary downtime.
Question 5: What tests are carried out during the DGUV-V3 test for low-voltage systems, and why are ISO measurements, loop impedance and checks on equipotential bonding and earth resistance so important?
Kevin Gering:
DGUV-V3 testing on low-voltage systems of wind turbines is crucial to ensure the safe and trouble-free operation of electrical systems. These tests not only help to prevent accidents, but also to avoid failures that could cause costly system downtime.
ISO measurements (insulation resistance measurements) are particularly important to check whether the electrical cables and components are correctly insulated. Inadequate insulation can lead to short circuits and dangerous electric shocks, which would jeopardize both the safety of employees and the functionality of the wind turbine.
The loop impedance test ensures that in the event of a fault, e.g. a short circuit, the protective mechanism (e.g. fuse or circuit breaker) responds quickly enough to prevent personal injury or damage to the system. If the loop impedance is too high, protective devices may not trip in time, which could have fatal consequences.
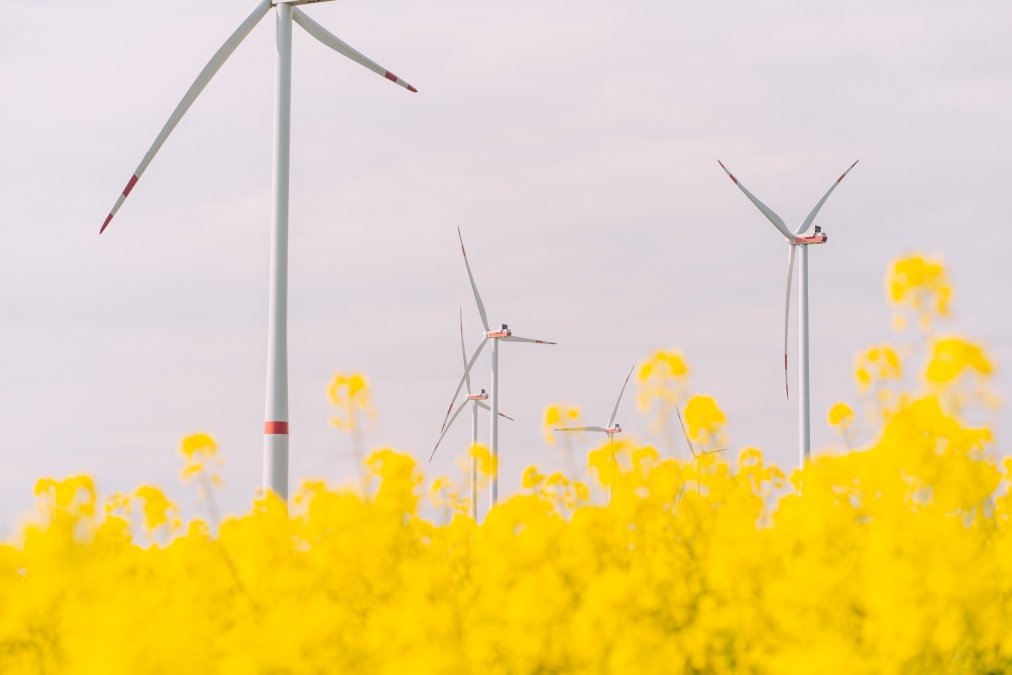
Checking the equipotential bonding is essential to ensure that all conductive parts of an installation have the same electrical potential. This prevents dangerous voltages from arising that could endanger people or equipment.
The earth resistance is measured to ensure that electrical fault currents can be safely discharged to earth. If the earthing resistance is too high, fault currents may not be discharged correctly, which increases the risk of electric shocks or damage to the system.
In addition, a visual inspection is always carried out during the DGUV-V3 test in order to detect and rectify obvious defects such as damaged cables or loose connections at an early stage. All of these measures serve to ensure the operational safety and longevity of the wind turbine and to meet legal requirements.
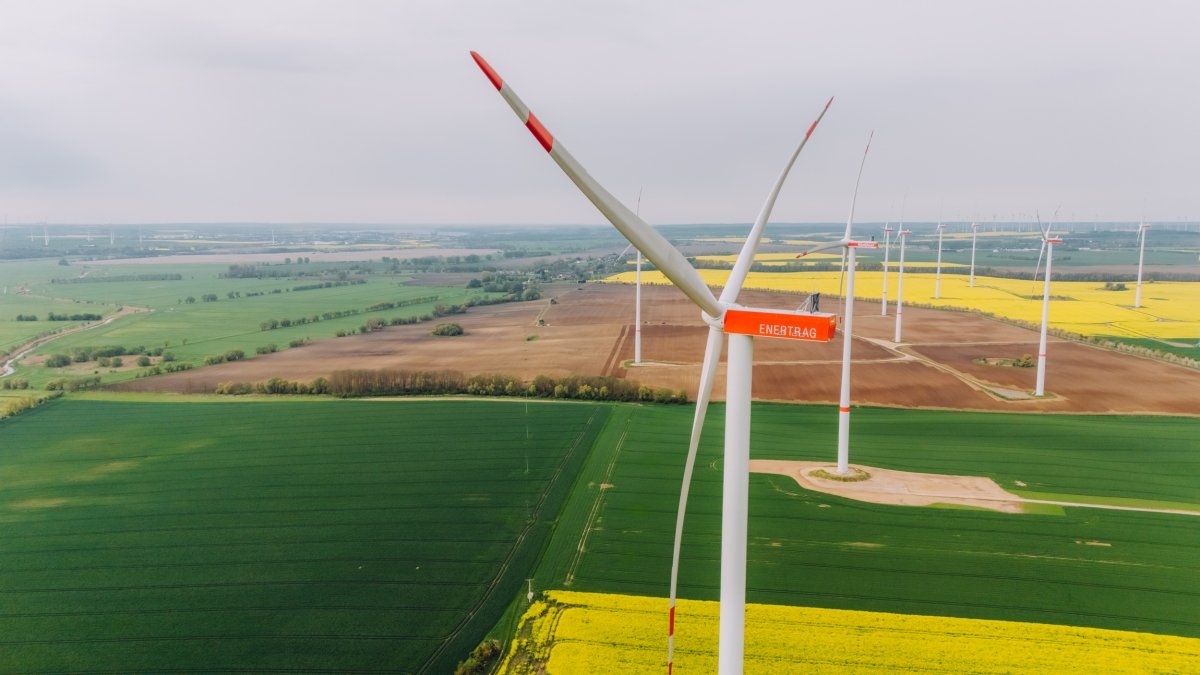
The DGUV-V3 test for medium-voltage systems ensures that all electrical systems work reliably and safely. The requirements for testing are particularly high in medium-voltage systems, as higher voltages are used here, which can lead to greater dangers. The main tests include
- Insulation resistance measurements: As with low-voltage systems, the insulation resistance of medium-voltage systems is also measured to ensure that there are no dangerous leakage currents that could lead to short circuits or voltage flashovers.
- Switchgear and transformer tests: These components are tested particularly intensively as they play a key role in energy distribution and control. The functionality and load capacity of the switching devices are tested here.
- Testing the earthing and short-circuit resistance: To ensure that the system is adequately protected in the event of faults such as short circuits, the earthing and the system's ability to safely discharge high short-circuit currents are checked.
- Visual inspection and mechanical check: A detailed visual inspection of the system components reveals obvious defects, such as mechanical damage or improper connections.
- Dielectric strength test: This tests whether the system remains stable during voltage peaks and whether there are no insulation defects.
The protective device test plays a particularly important role in the testing of medium-voltage systems. Protective devices are used to protect the system in the event of a fault and to switch it off in good time. Various tests are carried out here:
- Tripping time and current: It is checked whether the protective devices trip correctly and within the prescribed time in the event of an overload or short circuit.
- Protection settings: The setting of the protection devices must correspond to the grid parameters and the requirements of the system. It is checked whether they are correctly programmed and calibrated.
- Function test: This tests whether the protective devices trip reliably in the event of simulated faults, such as overcurrent or earth faults.
The protective device test is particularly important, as faulty protective devices could lead to serious damage or even the failure of the entire system in an emergency.